Sand making machine is used to produce artificial sand by crushing rocks. It is commonly installed after the cone crusher as a shaping equipment for secondary crushing. Regular maintenance can extend its service life and increase production.
Common faults and solutions of sand making machines
Fault 1: Abnormal vibration
Causes of failure
- 1Clear the blockage and clean the crushing cavity. Strictly control the size of materials, and large particles cannot enter the sand making machine.
- 2Excessive particle size of the feed material, leading to overloading of the equipment.
- 3Severe wear of the impeller and bearings causing imbalance within the machine.
- 4Loose bolts in the foundation or gear bolts.
Corresponding solutions
- 1Clear the clogging and clean the crushing chamber. Strictly control the specifications and moisture content of the feed.
- 2The material needs to be crushed again or a screen added to reduce the size of the material.
- 3Repair or replace excessively worn impellers and bearings, and regularly inspect the equipment.
- 4Tighten loose bolts and perform regular maintenance.
Fault 2: Bearing temperature is too high
Causes of failure
- 1The bearing lacks grease or the quality of the grease is not up to standard.
- 2Foreign matter and dust enter the bearing.
- 3The bearing has been used for too long and is seriously worn.
Corresponding solutions
- 1Replenish or replace grease in time. It should be noted that incompatible greases cannot be mixed. If you want to replace new grease, you must first clean the old grease on the bearings and then add new grease.
- 2Clean foreign objects and bearings. If foreign matter enters the bearing due to damage to the oil seal, the oil seal needs to be replaced.
- 3Regularly check the usage of bearings, record the usage time of bearings, and replace worn bearings in time.
Fault 3: Material blockage
Causes of failure
- 1The material is too large in volume or has too much water content, causing it to adhere to the inner wall of the machine.
- 2The feeding speed is too fast, and the crushing speed is not as fast as the feeding speed, causing blockage.
- 3Improper tightness of the V-belt results in the inability to transmit power to the sheave and the stone cannot be crushed.
Corresponding solutions
- 1First crush the material to the size that meets the input material or preheat it to remove moisture before sending it to the sand making machine.
- 2Adjust the feeding speed to ensure uniformity and continuity.
- 3Adjust the tightness of the V-belt to drive the sheave.
Fault 4: Sudden machine shutdown
Causes of failure
- 1Material blockage causing the machine to shut down.
- 2Low voltage unable to meet the requirements for normal machine operation.
- 3The main shaft is broken or the bearing is locked.
- 4The V-belt is too loose or severely worn, resulting in insufficient power transmission and the machine cannot operate.
- 5Equipment connection line breakage or poor contact preventing power transmission to the equipment.
Corresponding solutions
- 1Clear the blockage in the crushing chamber and control the feed particle size during subsequent feeding processes.
- 2Adjust the equipment voltage and restart the machine.
- 3If the main shaft is fractured, it needs to be repaired or replaced with a new one. If the bearing is seized, check if it was caused by excessive rotational speed. If damaged, replace the bearing.Improper grease addition can also cause bearing seizure, so follow the instructions and add an appropriate amount of lubricating grease.
- 4Use professional tools to adjust the V-belt, ensuring proper tension or replacing it with a new one.
- 5Regularly inspect the equipment's connection lines for integrity and ensure secure connections. If any damage or looseness is found, promptly repair or replace them.
Fault 5: The discharging particle size becomes larger
Causes of failure
- 1The looseness of the V-belt leads to a decrease in transmission efficiency, which makes the sand making machine's speed unstable, the number of material crushings reduced, and the discharge particle size becomes larger.
- 2The impeller speed is too high, causing the material to be thrown out of the equipment without being fully crushed.
- 3The feed particle size is too small, close to the required discharge particle size, resulting in few material crushing times. Or the feed particle size is too large, exceeding the processing capacity of the sand making machine, which reduces the residence time of the material in the equipment and increases the discharge particle size.
Corresponding solutions
- 1Turn off the sand making machine and adjust the tightness of the V-belt.
- 2Adjust the impeller speed to crush the material evenly.
- 3Reasonably control the feed particle size.
Fault 6: Abnormal noise occurs during operation
Causes of failure
- 1Failure or damage of bearings and gears leads to increased friction of parts and produces abnormal noise.
- 2Impeller and rotor are unbalanced or loose.
Corresponding solutions
- 1Stop the machine and check the bearings and gears. If damaged, new parts should be replaced.
- 2Balance and adjust the impeller and rotor, and tighten the relevant connecting bolts.
Fault 7: Oil leakage from the upper and lower ends of the shaft
Causes of failure
- 1Seals such as shaft seals or sealing rings are damaged, causing oil to leak from the seals.
- 2Failure of the lubrication system causes the oil to fail to flow normally, causing oil leakage.
Corresponding solutions
- 1Replace the seal with a new one and install and tighten it correctly.
- 2Check the lubrication system to ensure that the pipeline is not blocked. Clean filters and pipes if necessary.
Fault 8: Lubricating oil failure
Causes of failure
- 1Lubricating oil deteriorates.
- 2The lubricating oil pipe is blocked, causing the lubrication system to lose its lubrication effect.
- 3Improper selection of lubricating oil.
Corresponding solutions
- 1Keep the lubricating oil properly and seal it well to avoid direct sunlight or the entry of foreign matter.
- 2Clean the oil pipe and remove blocking materials.
- 3Lubricating oil with good adhesion and good vibration damping performance should be selected.
How to maintain the sand making machine?
The most effective way to maintain the sand making machine is regular parts maintenance and equipment cleaning.
Maintenance of parts
Bearing, rotor, impeller and impact block are important components in sand making machines.
In order to ensure that the sand making machine equipment is always in good performance and thus ensures continuous and effective production, it is vital to maintain these wear-prone parts.
Bearing: Bearing needs to be lubricated regularly and checked for oil leakage. Replace heavily worn bearing promptly. Immediately stop the machine for inspection if abnormal conditions such as high temperature or impact sound are detected. Adding a rubber plate of suitable thickness between the bearing seat and support frame can reduce bearing load.
Rotor: Regularly clean the surface and interior of the rotor, and check the tightness of bolts, bearing seats, and other components on the rotor. Ensure that the tightness and length of the V-belt are appropriate, as improper tension can lead to rotor imbalance. Additionally, it is necessary to periodically perform balance calibration on the rotor.
Impeller: Check for any foreign objects in the impeller before starting the machine to prevent motor issues. Excessive material can cause imbalance and wear, so ensure uniform and continuous feeding.Stop feeding before stopping the machine to avoid impeller damage. Promptly replace worn impellers for normal production operations.
Impact block: Adjust the gap between the impact block and the counterattack plate in time. An appropriate gap can provide a certain buffering and protection effect, which helps to reduce equipment wear.
Equipment cleaning
In addition to maintaining key components, cleaning equipment can effectively remove harmful substances and reduce malfunctions.
- Shutdown and power outage: Ensure the sand making machine is properly shut down and the power supply is disconnected for safety.
- Clean the materials: Use shovels and brooms to remove any materials, such as sand and gravel, from the equipment to prevent residue buildup.
- Clean the screen: Use a water gun or water pipe to flush the screen to remove clogged impurities.
- Clean the conveyor belt: Use a damp cloth or brush dipped in water to clean the surface of the conveyor belt to remove attached sand, gravel and dust.
- Clean the body and machine surface: Use a damp cloth or brush dipped in water. For stubborn dirt or deposits, use an appropriate cleaning solution or acid-base solution if necessary.
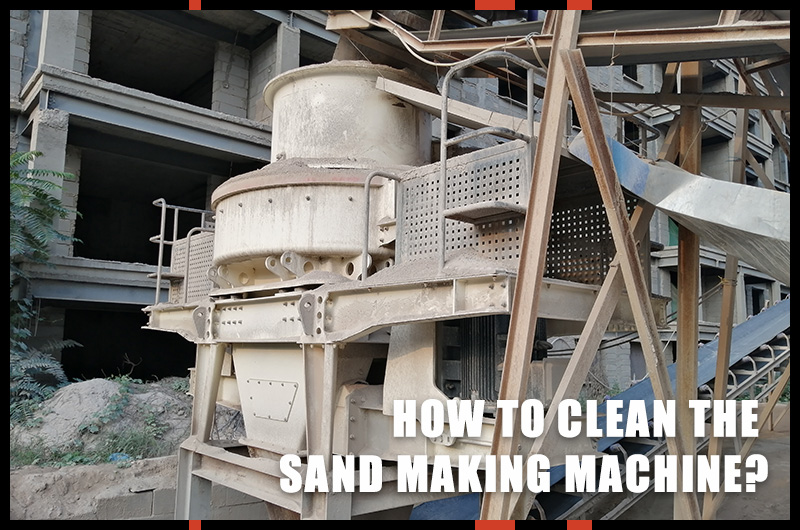
Different sand making machine models and materials may have specific requirements and restrictions regarding the ratio of detergents and acid-base solutions.
It is recommended to consult a professional repairman or FTM engineers for accurate guidance.Contact us
Conclusion
FTM Machinery is a reliable sand making machine manufacturer. Our sand making machine offers high output of up to 650 t/h, increases material throughput by 30%, and reduces power consumption by 10-40%. Choose us to improve the sand making efficiency of your factory!