Cement, made by calcining and grinding limestone and other raw materials, is the most widely used building material. As a professional cement company, FTM Machinery offers expert guidance for your cement production.
How to Make Cement?
The manufacturing of cement (such as Portland cement (OPC)) usually go through 5 major processes:
How is cement made?
1. Prepare cement raw materials: The primary raw materials are limestone and clay, along with fly ash, iron ore, and coal.
2. Grinding: The raw materials are ground into fine powder (1–25 mm) using crushers and mills. Typical ratios: 67–75% limestone, 10-15% clay, 0.5–1.5% iron ore, and 8.5–11% coal.
3. Calcination: The raw meal is preheated to 900°C and then heated to 1450°C in a cement kiln to form cement clinker.
4. Clinker cooling and final grinding: The clinker is cooled to 120°C and sent to the cement mill for final grinding, with 5% gypsum added to control solidification.
5. Storage and Packaging:The powdered cement is stored and transported in bags for concrete production.
Key Cement Equipment
If you want to manufacture cement, choose equipment carefully as it affects cement quality. The cement industry now prioritizes the efficient, energy-saving, and eco-friendly cement machine.
A popular cement plant includes the cement crushers, raw material mill, cement kiln, cooler, cement mill, dust collector, cement separator, and cement packaging machine.
1. Equipment for Cement Raw Material Preparation
- The cement crushers are used to crush raw materials into smaller sizes.
- Four types of crushers are available: jaw crusher, cone crusher, impact crusher, and hammer crusher.
- Jaw crusher: Primary crusher; handles any hardness and moisture, feed size up to 1,200 mm.
- Cone crusher: Secondary and tertiary crusher; crushes hard materials, discharge size within 40 mm.
- Impact crusher: Secondary and tertiary crusher; crushes soft materials, discharge size 2–10 mm.
- Hammer crusher: Coarse, medium, and fine crushing; discharge size within 40 mm.
- Raw Material Mill is the key equipment for grinding cement raw materials and other materials after crushing.
- Feeding size:<25 mm
- Capacity: 4.5–210 t/h
- Advantages: High grinding efficiency, large output, no dust pollution, energy saving, long service life.
③ Rotary Drum Dryer: $1,000/set (the lowest price)
- It is used to dry cement raw materials and other bulk solid materials.
- Power: 7.5–160 kW
- Capacity: 1.9–76 t/h
2. Equipment for Clinker Calcination
① Rotary Kiln: $1,000/set (the lowest price)
- The cement rotary kiln is the core equipment in wet and dry cement plants for producing clinker in cement.
- It is designed for harsh environments, with a long lifespan, using a burner at the kiln head to calcine raw materials with natural gas or coal.
- It ensures uniform heat distribution, low heat consumption, good sealing, and stable cement quality.
- Capacity: 180–10,000 t/d
- Rotary cooler machine is ideal for cooling clinkers and other bulk materials.
- It quickly cools cement clinker to below 200°C, enhancing quality and grindability.
- Power: 15–315 kW
- Capacity: 2–75 t/h
3. Cement Grinding Equipment
① Cement Mill: $5,000/set (the lowest price)
- A cement mill (usually a ball mill) grinds clinker and gypsum into fine cement powder, completing the final step of cement manufacturing.
- Feed size:<25 mm
- Output size: 325 mesh
② Coal Mill: $317,060/set (the lowest price)
- Coal mills are used to grind raw coal into fine coal powders.
- Feed size:<25 mm
- Capacity: 3–40 t/h
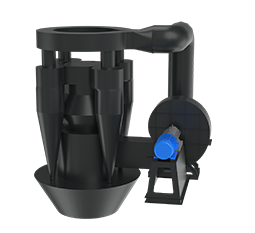
③ Cement Separator
- Provide advanced cyclone air separators as cement separators to select qualified cement and avoid over-grinding.
- Airflow: 16,000–240,000 m³/h
- Capacity: 10–250 tons/day
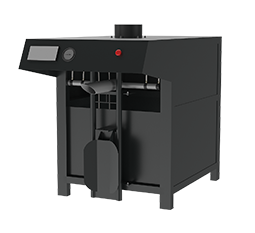
④ Cement Packing Machine
- It automatically packs bulk cement and powder materials with good fluidity (fly ash, cement additives, etc.) into bags.
- Number of nozzles: 6–12
- Packing speed: 1,200–3,000 bags/hour
4. Auxiliary equipment
① Conveyor Belt: $100/set (the lowest price)
- It is used for long-distance continuous material transportation.
- It moves in both directions and operates horizontally, diagonally upward, or downward.
- Simple operation, safe amd reliable, automatic unloading.
- Length: 10–50 meters
- Capacity: 30–3,000 t/h
- It is used to collect raw powder or cement finished products.
- It has large air volume, good dust collection effect and automatic control.
- Processing air volume: 864–252,000 m³/h
- It is used to produce quicklime (calcium oxide) by roasting active lime and calcined dolomite for steel mills and ferroalloy plants.
- It is the most commonly used type in most lime plants, with low energy consumption, good sealing, and air leakage coefficient below 10%.
- Capacity: 180–10,000 tons/day